Dokładność skanerów 3d – weryfikacja
Każdy ze skanerów 3D produkowany przez firmę SMARTTECH jest sprawdzany zgodnie z normą, natomiast dla klientów wymagających dodatkowej dokumentacji dokładność, system może być certyfikowany przez akredytowane laboratorium pomiarowe tym samym uzyskując referencyjność równą standardowej maszynie współrzędnościowej.
Certyfikacja a tym samym utrzymanie dokładności pomiarowej przez okres użytkowania skanera 3D jest możliwe tylko w przypadku skanerów skalibrowanych na stałe na daną objętość i posiadających szczelnie zamkniętą obudowę.
Dlaczego kalibrujemy skanery wg normy?
Wychodząc naprzeciw klientom firma SMARTTECH wprowadziła jako standard normowanie, wzorcowanie i kontrole skanerów 3D wg niemieckiej normy VDI/VDE 2634, stworzonej przez niemieckie stowarzyszenie Fizyków i Inżynierów. Norma ta jest czytelna i wymierna dla wszystkich, więc daje możliwość porównania i wybrania dla siebie najlepszego systemu skanowania optycznego 3D.
Wytyczne normy VDI/VDE 2634
Wytyczne określają następujące parametry:
-
błąd układu głowicy optycznej - wykonywany na pojedynczej kuli,
-
błąd wskazania długości - wykonywany na wzorcu ball bar,
-
błąd płaskości - wykonywany na płaskiej płytce.
Procedura postępowania
Pierwszy parametr
Opisuje on błąd charakterystyczny dla optycznych systemów pomiarowych 3D opartych na skanowaniu powierzchni w małym zakresie pomiarowym, czyli jest to: odległość między środkiem sfery wyznaczonej z zastosowaniem kryterium Gaussa (metoda najmniejszych kwadratów) – będącej elementem skojarzonym, opartym na skończonej liczbie punktów pomiarowych skorygowanym na tym samym kulistym wzorcu materialnym wymiaru – a punktem pomiarowym skorygowanym na tym samym kulistym wzorcu materialnym wymiaru.
Jako wzorzec stosowana jest kula o średnicy D z materiału odpowiednio rozpraszającego światło:
D = (0,1…0,2) L0
gdzie: L0 – przekątna mniejszego prostokątnego równoległościanu obejmującego przestrzeń pomiarową.
Procedura polega na pomiarze kuli w co najmniej 10 ustawieniach w całej przestrzeni pomiarowej.
Na kolejnym etapie, stosując funkcję „best fit” , wyznacza się promień kuli, a następnie oblicza różnicę między rzeczywistym promieniem skalibrowanej kuli a uzyskanym wynikiem. Operacje te wykonuje się oddzielnie dla każdej z 10 pozycji.
Dane oblicza się dla każdej z kul i wpisuje do tabeli.
Wynik przeprowadzonej próby będzie pozytywny wówczas, gdy żaden z błędów wpisanych do tablicy nie będzie większy od maksymalnej dopuszczalnej wartości, wynoszącej maks. 1/5 charakterystyki wymiarowej wzorca kuli, a za niepewność pomiaru uzna się najwyższą wartość z otrzymanych różnic.
Drugi parametr
Kolejnym wyznaczanym parametrem jest błąd wskazania długości, określany wzorcem „ball bar” (dwie kule wykonane z odpowiedniego materiału). Wymiary wzorców wynikają z zależności podanych na rysunku poniżej.
Schemat wzorca do testowania błędu wskazania długości:
Lp ˃ 0,3 L0Dp = (0,1…0,2)
L0L0 – przekątna prostopadłościanu opisującego zakres pomiarowy
Lp – odległość między środkami kul
Dp – średnica kuli
Parametr służy do weryfikacji prawidłowego odtwarzania przez skaner 3D długości. Według zaleceń VDI/VDE jest to różnica długości między wartością zmierzoną a wykalibrowaną (rzeczywistą) między środkami kul. Wyznacza się ją ze wzoru:
Δl = lm-lk
gdzie:
Δl – błąd odległości między środkami kul
lm – zmierzona wartość długości
lk – wzorcowana wartość długości
W celu wyznaczenia parametru należy zmierzyć wzorzec pomiarowy w pozycjach.
Do każdej z dwóch kul wzorca za pomocą funkcji „best fit” dopasowana zostaje sfera. Automatycznie w programie Mesh3D, wyliczony zostaje promień sfery oraz jej współrzędne środka.
Mając te dane możliwe jest obliczenie wartość długości między kulami i ze wzoru wyznaczany jest błąd odległości.
Podobnie jak przy pierwszym parametrze, wartości nie powinny przekraczać 1/5 wymiaru sprawdzanego we wzorcu. Jako niepewność tego parametru wybiera się najwyższą wartość.
Trzeci parametr
Ostatnim wyznaczanym parametrem jest błąd płaskości powierzchni.
Wytyczne VDI/VDE definiują go jako zakres odległości punktów zmierzonych od płaszczyzny skonstruowanej metodą najmniejszych kwadratów. Wzorzec wykonany jest z materiału o niskiej refleksyjności, którego szerokość nie może być mniejsza niż 50 mm, a długość - od 50% przekątnej bryły opisującej zakres pomiarowy.
W celu wyznaczenia błędu płaskości należy wykonać pomiar w 6 pozycjach.
Następnie, stosując opcję „best fit”, wyznaczyć próg niepewności dla wszystkich pozycji i obliczyć różnicę między wartościami: wzorcową i otrzymaną z opcji dla każdej pozycji wzorca.
Błąd płaskości nie powinien być większy niż 1/5 mierzonej charakterystyki. Wybieramy najwyższą wartość, która stanowi o niepewności pomiaru urządzenia.
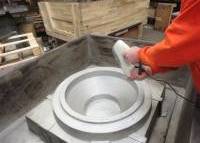
Wykorzystanie skanera 3D Eva w odlewnictwie
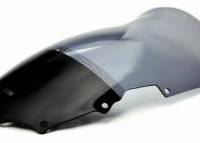
Zastosowanie optycznych skanerów 3D - Tuning
